Do you feel that the execution of your lighting design doesn’t always go as planned? One of our main roles as designers is to mitigate risks throughout the project and having an efficient process in place for project objectives helps to mitigate risks. Since lighting design plays a huge role in every project from how the space is lit to shaping the wellbeing, health, and mood of occupants, it is important that all stakeholders work together during the execution process.
Through our experience, and through speaking with multidisciplinary experts, we have identified repeating issues on projects related to the execution of lighting design. To combat these issues, we have created a process for ‘new lighting design’ in interior spaces that we find works well and leads to successful projects. We have outlined this process below and hope that others in the community can use it to generate more success in their projects.
Pre-construction & Design Stage
- Kickoff Meeting with Supplier
It is beneficial to have a kickoff meeting with the lighting supplier right at the beginning of your project, in order to explain project details including the scope of work, budget, and timeline.
- Budget
It is extremely important to establish a rough ‘Full Project Budget’ at the beginning of the project in order to set cost boundaries and avoid the potential risk of needing to re-design the lighting as a result of avoidable cost overages. The lighting budget can be estimated through collaboration with your lighting supplier and using past project experience.
- Timelines
In most cases, the project end date is established (or at least estimated) at the beginning of the project. It is important to share timelines with your lighting supplier such that you can choose main light fixtures that work with the timeline. Remember, lead times are based on when an order is approved and released (electrical distributor needs to give the go-ahead to release the project for manufacturing) which can take anywhere from four days to two weeks, depending on the project size. In your project schedule, you can map out key lighting deadlines from the design stage to construction, such that you identify the maximum lighting lead times for the project.
- Figuring out all the details
Your lighting supplier is an expert in their products. Make sure to work with your lighting supplier to finalize each type of light fixture in each area. Provide your supplier with all project details, such as type of application, ceiling heights and types, colour scheme and material types (which impact the lighting calculations), concept presentation, the type of mood you are trying to achieve in the space, and if the fixture needs to be on an emergency circuit (which the engineer will advise).
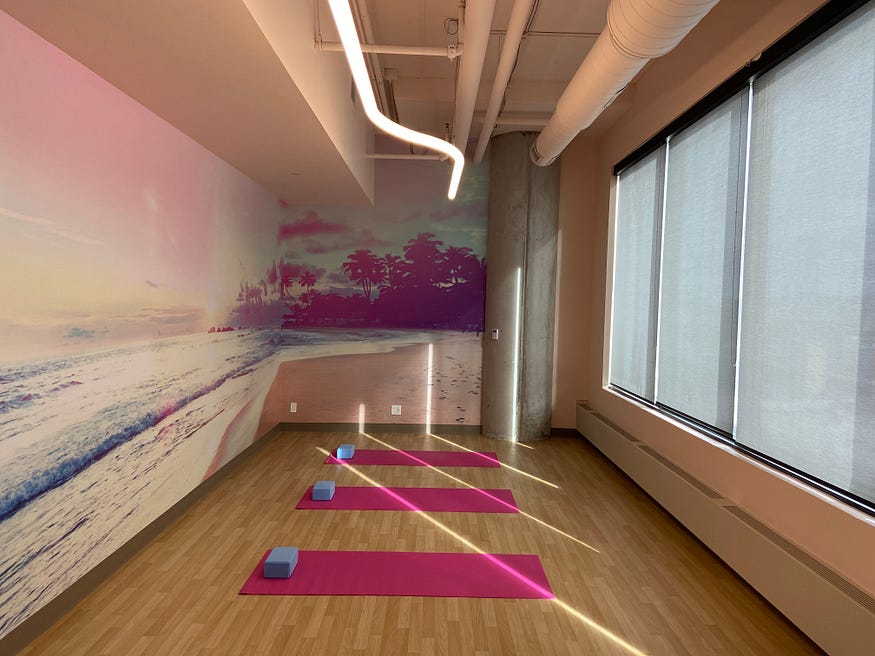
The next step is to receive lighting calculations and cut sheets and to work with the supplier to review all the details of each light fixture such as colour temperature, fixture colour, suspension type, driver location, etc. Don’t forget to discuss lighting controls! Today, there are many different types of controls that can help reduce the number of switches needed while still providing the flexibility to control a variety of zones. Upon finalizing light fixtures and lighting calculations you should receive all of the fully completed lighting cut sheets which you can forward to your electrical engineer. The electrical engineer can finalize any remaining details with your supplier.
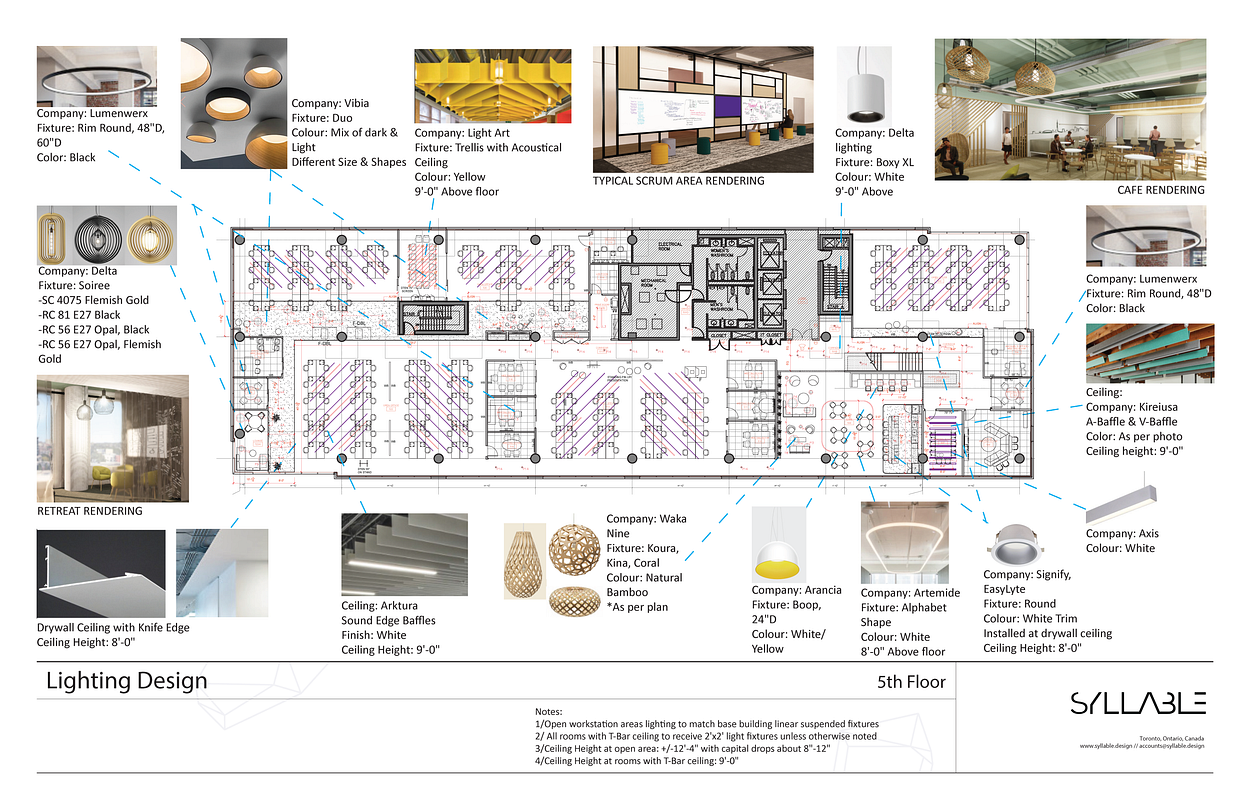
- Construction Drawings
Ensure the engineer completes the luminaire schedule and makes sure to share the schedule with your lighting supplier for final review. To reduce coordination hours with the contractor/electrician, in the interior designer’s drawing set make sure to provide an RCP with mechanical and electrical items overlaid. This will help identify any interference that may require adjustment and will allow each on-site trade to see the full extent of the required work, including the other elements that need to be taken into consideration during the installation.
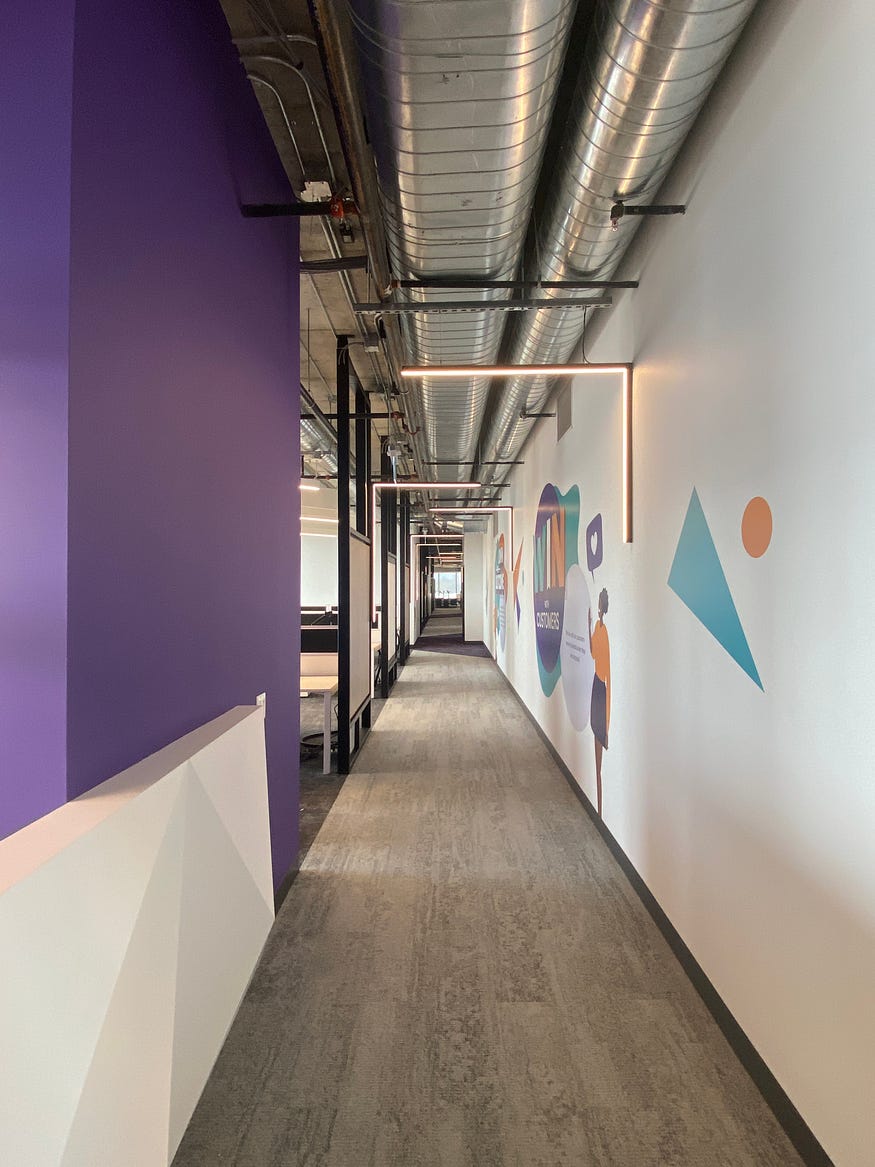
The overlaid plan is mostly helpful in an open ceiling design or complex ceiling design, but it is also beneficial to get in the habit of doing this for all projects. In the Interior Designer’s Lighting Specifications, it is also helpful to include a ‘lead time’ column and denote each fixture’s lead time and estimated shipping time relative to when the approved shop drawings are received by the supplier. Finally, it is important to identify the suspended height of each light fixture, and any fixture height that needs to be reviewed on site.
Contract Administration Phase
- Kickoff Meeting
One item that has been identified as an ongoing issue during projects is the lack of communication between all stakeholders involved. It is important for the General Contractor to set up a quick kickoff meeting that includes key players, such as the supplier’s project manager, distributor, electrician, and designer. This meeting will serve to introduce everyone who will partake in the lighting design and execution process, create open communication, allow for the discussion of any special instructions needed for lighting installation, make everyone accountable for their actions, and establish a team atmosphere.
- Purchase Orders
It is important that the contractor ensures the PO for lighting is received by the supplier quickly so shop drawings can be released. During the kickoff meeting, long lead items and order dates can be identified up front. It is important for the supplier to stay on top of this process to ensure they receive the PO right away and keep the team up to date.
- Shop Drawings
Shop drawing processing can be unnecessarily long and impact the delivery of your light fixtures. During the kickoff meeting, the processing method for your project should be discussed and established. One method that has been successful for us involves the supplier’s project manager sending shop drawings directly to the consultant with all required stakeholders (distributor, electrician, contractor) copied on the email. This process can eliminate shop drawings sitting in email inboxes for days avoiding project delays.
- Installation
The electrician should inspect all lighting and specified quantities right when the product is received such that they can coordinate with the designer and lighting supplier for any missing or defective parts and to review any special lighting installation requirements. Throughout the installation, suppliers and designers must quickly work together to resolve any issues that may arise. It is also very important for the electrician to chalk out lighting layouts prior to beginning installation for complex lighting patterns and to quickly identify any interferences that must be resolved by the designer. All specialty lighting heights should be finalized with the designer on site prior to construction ending.
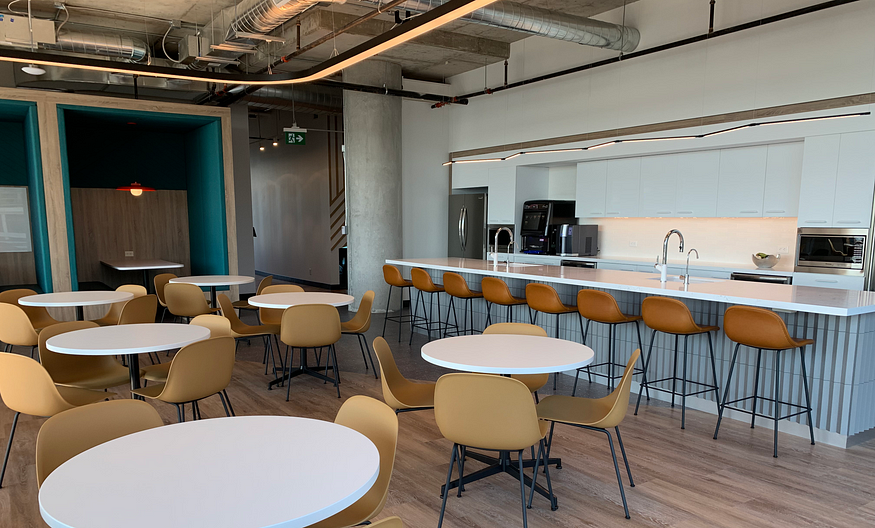
Every project — small, medium, and large — must be an effort that leverages the expertise of the whole team to ensure success. Consistency in the process and establishing trust between stakeholders is critical to mitigating project risk. The above-mentioned process is one that has worked well for our team in the past. We learn from each of our projects allowing us to continuously revise processes that keep us on the leading edge of an ever evolving industry.